After I have published an article about the price of Podbike, respectively their model Frikar, in the discussions on Facebook there have appeared many questions about this interesting vehicle. To some of them an answer can be found on the Podbike website, and some I asked directly in Norway and got long answers from Janet Usken, who is in charge of Public Relations in Podbike.
How will you solve warranty repairs and other service issues outside Norway?
As you probably are aware, Podbike is a startup velomobile company, and to be able to sell our velomobile for a reasonable price we have decided to not use dealers, at least not in the initial phase. All sales are on-line and we only sell FRIKAR as a self-assembly kit, as clearly stated in several places on our webshop.
You must assemble your own FRIKAR. So initially we are only targeting velomobile riders who are capable of doing the assembly themselves. Fortunately, as most of the assembly work has been done by us, the final assembly should not be difficult or very time-consuming, we estimate between five to ten hours, depending on how good you are in assembling a kit. Experienced IKEA furniture and Lego builders will definitely have an advantage.
That means the first FRIKAR riders will have to replace parts themselves, both parts under guarantee and regular wear items like brake pads and tires. However, we promise to provide excellent service documentation and fast delivery of spares. If you are unable to do repairs yourselves, you should wait to purchase FRIKAR until we have service partners in place near you. We are in discussions with potential service partners in different countries but those agreements are still to be settled.
Can you give us more information about the motors?
We use three identical brushless PM motors, one for each rear wheel and one for the pedal generator. One rear motor is driven by the battery, and the other rear motor is driven by power from the pedal generator. Each motor is controlled by its own dedicated motor controller that is mounted on a pressure-cast aluminum motor bracket together with the motor. The motor can not spin without the controller generating the correct waveforms so the motor and the controller are acting together as a unified system. The motor bracket also acts as a heatsink and is equipped with a small electric fan so we can climb even steep hills with small motors with only 250W nominal power, as required by EU legislation for Pedelecs. In case there is a failure in one motor system, the other takes over, however with less available power.
What is the loss of power when you transmit it via generator/cables/motors?
In percent, it is quite a lot. Measured in Watt it is not much. Most people are only capable of average leg power output between 50-100 W. So even with only 50% efficiency, the driveline losses can easily be compensated by a few hundred grams of extra battery per hour of cycling.
The low efficiency of our driveline does not look good on paper. But as a compromise, the reduced efficiency is well compensated by much lower parts cost and less costly and time-consuming maintenance. We have been very rough with some of our test bikes. One has never been washed, even after riding it in pools of road salt. But the efficiency is as low as normal, not lower, and it still works. But please note: Even though we use aluminum alloys rated for use at sea, you should wash away road salt several times during the winter as some of the road salt mixtures are even more corrosive than regular seawater. I just mentioned this as an example of one of several internal torture tests we use to stress test our engineering solutions.
Did you solve the issue with way too long delay between the start of pedaling and the start of movement of the vehicle as seen in the early videos?
The test bikes differ from the upcoming production vehicle design on many levels, this is one where there will be a huge difference between test bikes and production versions. We have a new motor with higher torque and a larger transmission ratio so we should be able to provide 2-3 times higher torque. Both on the pedal generator and on the rear wheels. Also, the control algorithms have been rewritten providing much better feedback to the cyclist.
In addition, the bike you receive will become better as we refine the FRIKAR software. All the software on the bike (except for the BMS board inside the battery) is automatically updated with the bike mobile phone app.
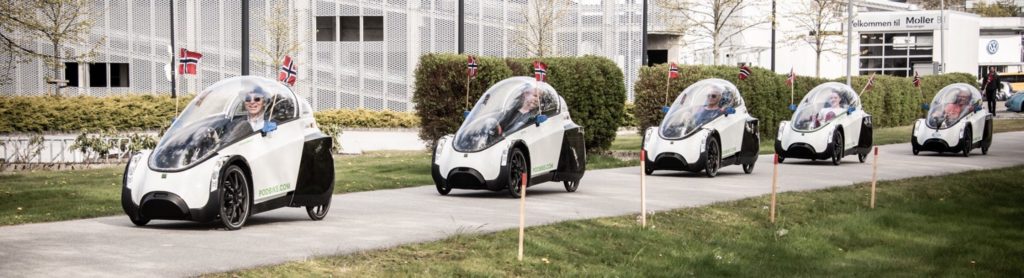
Can you explain how you can achieve such a low price when other velomobiles with electric engines are usually double the price?
We do several things differently from others to cut the cost of our velomobile compared to others. Firstly, we do not make a finished velomobile. We make a flat package that you have to assemble yourselves, just like IKEA furniture. And most options you will need to assemble and install yourself. We also leave out profit to the dealers. We also ask you to replace defective parts under warranty instead of going to a repair shop. All this cuts a lot of costs.
We made our own driveline, tailor-made for this vehicle, based on off-the-shelf motors, avoiding expensive OEM branded motors. Then we used the first principle design on how to make as low-cost a transmission as possible while maintaining low unsprung mass, and very long life as that is required to provide environmental sustainability.
Then we have been working ten years on developing the product, building brick by brick with a focus on safety, practicality, and cost while trying to make as good looking yet sustainable a product as possible. We have been working very long hours and be extremely focused on making the world’s most sustainable vehicle for personal transport. And we are continuously working on improving the product along different performance axes.
Finally, most velomobiles currently for sale are optimized for speed. To make a really fast velomobile you must make it light and with minimum CdA (drag coefficient, Cd, times the frontal area A). And one of the best ways to achieve this is to construct an aerodynamic monocoque from fiber-reinforced thermosets and make a low and as narrow-body as possible. Since the velomobile needs to suit the human body inside while keeping the frontal area to a minimum, many velomobiles are tailor-made for a specific person, just like bespoke racing bike frames. However, the use of expensive materials and low volume production drives up cost. In addition, most velomobiles are not made on an industrial basis but as handcrafted speed machines with many labor-intensive operations. Our FRIKAR® velomobile is optimized for practicality and cost, not speed. If you prioritize speed and want a really fast velomobile, a conventional tadpole design from someone else is probably a better alternative.
Are there still mechanical and also hydraulic brakes used? Why there are two types?
We use hydraulic disc brakes in the front because they give the best braking performance including matching of left and right brake torque. We use mechanical disc brakes in the rear as we need good parking brakes that can be trusted over time. We decided to not use hydraulic brakes for parking due to the risk of minute leaks due to wear causing parking brake failure.
And here are the questions to which answers can be found on the Podbike website. Yes, you need to dig a bit deeper sometimes.
How tall/small riders fit in the Podbike?
Riders from 150 to 200 cm can ride the vehicle.
What is the range of the vehicle?
We will offer single 100 Wh battery modules that extend the battery capacity. Currently, we plan to provide space to fit up to 15 modules in total, with up to 300 km range.
Why did you decide to have the serial drive train with no connection between pedals and wheels?
Electronic transmission is a very important part of Frikar’s construction. It removes the chain and the gearing, two of the most service-intensive parts on a velomobile, and often the dirtiest as well. In addition, it simplifies the complexity of powering more than a single wheel on a velomobile. Having two motors adds little complexity to an electronic solution, and the added redundancy results in a more fault-tolerant propulsion system.
How is it possible that the bike has two motors, can reach a higher speed than 25 km/h and why do you mention also a maximum speed of 60 km/h?
We use three motors/ generators, two that act as electronic transmission and one that acts as assist motor/electronic brake. The power to the assist motor is limited to 250 W continuous output and 25 KPH speed limit, while the other motor output matches the pedal generator input thus acting as the human-powered transmission. This motor works beyond 25 KPH. However, when you use the electronic brake that can be triggered manually, for example by pedaling backward while going forward, or automatic when reaching max downhill speed, both wheel motors brake the vehicle.
The assistance to speed from the battery is limited to 25 KPH. However, the pedal generator is not. So by continuing to pedal and thus supplying manmade pedal energy, speed may increase beyond assist speed depending on various factors like inclination, generator output, efficiency, and rolling resistance. However, the max speed will be limited to 60 KPH for safety reasons. We store pedaling energy and braking energy using electric batteries. We do not use mechanical flywheel (s).
And if you still have some more questions, here is the complete FAQ or Master Thesis Velomobile: Redifined by Per Hassel Sørensen, the product developer of Podbike